How Can Workers Avoid Being Injured in a Forklift Accident?
July 16, 2022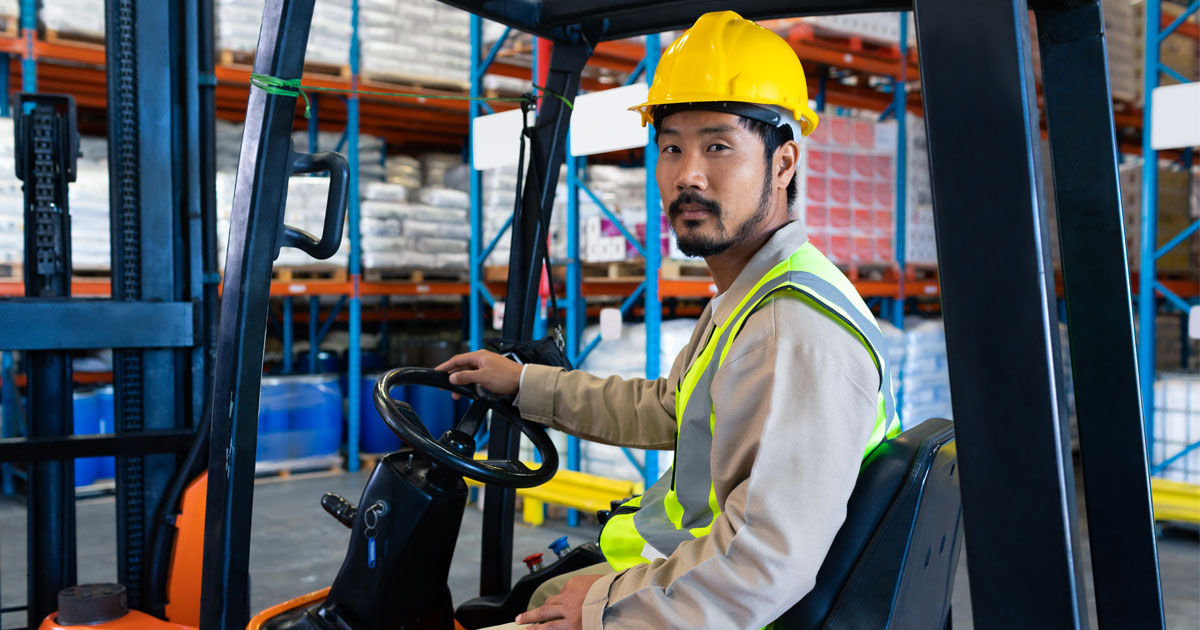
The warehouse industry has some of the highest rates of workplace injuries and fatalities, with falls, rack collapses, getting caught between objects, and falling debris causing some of the most serious, often fatal, injuries. Machinery accidents also cause devastating personal injuries at warehouses, particularly if the necessary safety protocols are not being followed, or workers have not been properly trained on how to operate the machine. Forklifts are one example of a type of machinery that can cause very serious injuries to the person operating the machine, as well as other workers in the vicinity. Although there are proactive steps that employers and warehouse workers can take to prevent these potentially devastating injuries, these injuries will continue to occur if employers do not make safety a top priority and ensure that all workers are properly trained. If you have suffered a serious injury in a forklift accident, do not hesitate to contact a lawyer experienced in Workers’ Compensation.
What Are the Most Common Types of Forklift Accidents?
Each year, approximately 97,000 warehouse workers are injured in forklift-related accidents in the United States. Roughly 100 of those injuries result in devastating fatalities and another 20,000 involve serious injuries that cause employees to miss weeks or more of work. According to the Occupational Safety and Health Administration (OSHA), 25 percent of forklift accidents occur because workers were not properly trained on how to operate the machine, which is a problem because it means that many of those accidents could have been prevented. The following are additional examples of some of the most common causes of forklift accidents:
- When forklift operators become too comfortable operating the machine, they are more likely to drive too fast around the warehouse. OSHA recommends that forklift operators should maintain a 5 mph or less speed when driving the forklift around the facility. Speeding shortens the amount of time that forklift operators can react to an unexpected situation and increases the risk of a serious accident.
- Operating a forklift with an elevated load. Too often, forklift operators will load the cargo they are lifting and elevate it a bit too high. This is dangerous for a couple of reasons. If the load is blocking the operator’s view, he or she could hit a worker who is in the general vicinity of the forklift. In addition, when a forklift has an elevated load, it is more likely to tip over, which can cause the forklift operator and other workers in the vicinity to become seriously injured.
- Improper turning. Forklifts are prone to tipping because the machine turns with the rear wheels, which causes the rear end to swing outward. Forklift operators should use caution when turning because there is an increased risk of tipping, particularly when workers make tight turns.
- Riding a forklift or giving someone else a ride. Forklifts are designed specifically to lift and move cargo from one place to another. Although it may seem harmless to hop on a forklift that is being operated by another worker, this is actually very dangerous, even if you are using your arm or another part of your body to balance the load.
- Unbalanced or unsecured loads. When the cargo is not loaded evenly, there is an increased risk of tipping over. In addition, if the cargo is not secured properly, it can fall off the forklift. Depending on the type of materials that fall off the forklift, this can cause serious injuries to workers if they get hit by falling cargo.
- Knocking off a pallet. Operating a forklift looks easier than it is. Picking up and setting down a pallet can be tricky, particularly if the operator’s view is obstructed by the pallet.
- Operator error. If the forklift operator is tired, distracted, or simply careless, they could hit another worker who is walking by or doing other type of warehouse work. If a worker is hit by a forklift, they are likely to suffer severe, even fatal, injuries.
- Mechanical failure. If the forklift has mechanical issues, it is more likely to malfunction and cause problems that could result in serious injuries. The forklift should be inspected at the beginning of every shift. Workers should follow a forklift inspection checklist to ensure that the machine is in good working order. Any repairs that need to be made should be done before the forklift is used again.
What Are the Best Ways to Prevent a Forklift Accident?
There are a range of safety protocols that must be followed when operating a forklift. Warehouse workers are responsible for following these safety protocols, and employers are responsible for providing the necessary training and enforcing the safety requirements. By making safety a top priority and taking the following safety measures, serious, even fatal, injuries can be prevented:
- Provide the necessary training. Companies are required to have a training program in place for forklift operators. However, companies are urged to provide additional training to employees who work in the vicinity of forklift. In addition, it is highly recommended that companies provide annual refresher training to ensure that all employees are aware of the safety protocols and that they are trained on any new equipment or safety measures.
- Make sure that the warehouse is clean and organized. If there is debris on the ground, or any other materials or spills that could cause the driver to have to make a sudden or erratic movement to avoid them, this could lead to an accident. Floors should be clean, dry, and well-lit always. Light bulbs that burn out should be replaced immediately.
- Inspect the machinery on a regular basis. Employers should conduct routine safety inspections of all forklifts and other machinery that is used in a busy warehouse. The inspection should check for any leaks, including fuel, hydraulic oil, engine oil, and radiator coolant; as well as tire pressure, engine belts, hoses, and the actual fork mechanism. If any repairs need to be made, they should be done before the forklift resumes operation.
- Follow the recommended loading and unloading procedures. Unevenly loaded or poorly secured cargo either comes loose or causes the forklift to tip over. All pallets should be uniformly stacked, and the stacked height and overall weight should be considered when building pallets.
- Use the appropriate personal protective equipment (PPE). All forklift operators should be required to wear hard hats, reflective vests, and other PPE, which should be provided by the employer.
- Use a fork leveler. Certain models of forklifts are equipped with an automatic leveler that resets empty forklifts to a level position simply by pressing a button.
- Set up signage around the warehouse. This will help encourage forklift operators to use caution when operating any type of machinery and remind them to make safety a priority at all times.
- Limit the use of forklifts in pedestrian areas. Forklift operators should avoid using this type of machinery in areas where there is a significant amount of pedestrian traffic, including break rooms, restrooms, food serving areas, and main exits. In addition, forklift operators should never assume that a pedestrian is aware of the forklift and move out of the way. Employers are urged to establish aisles that are designated for forklift operators and those that are for pedestrians.
- Use extreme caution when maneuvering blind spots and corners. It is the forklift operator’s responsibility to alert pedestrians that they are approaching a corner or blind spot. They can do this by using their horn, flashing their lights, or applying the backup alarms. Overhead dome mirrors can also provide improved visibility for pedestrians when they are approaching a corner.
- Use barriers to isolate forklift workstations. This will help keep workstations safe and protect pedestrians and other workers from the hazards associated with forklifts. This has been proved to reduce the number of pedestrian accidents that occur in warehouses.
What Should I Do if I Am Injured in a Forklift Accident?
The first thing you should always do if you suffer any type of workplace injury is to seek immediate medical attention. Next, you should inform your employer or supervisor that you have been injured in a forklift accident. Once you have notified your employer, you will need to file a Workers’ Compensation claim so that you can start receiving benefits while you are recovering from your injury. If you have questions about the claims process, or your claim has been denied, contact a Workers’ Compensation lawyer as soon as possible.
Baltimore Workers’ Compensation Lawyers at LeViness, Tolzman & Hamilton Help Workers after Forklift Accidents
If you suffered a serious injury from a forklift accident, do not hesitate to contact the Baltimore Workers’ Compensation lawyers at LeViness, Tolzman & Hamilton. We will walk you through every step of the claims process, address all your questions and concerns, and ensure that you receive full and fair compensation for your injuries. Call us today at 800-547-4LAW (4529) or contact us online to schedule a free consultation.
We have offices in Baltimore, Glen Burnie, and Prince George’s County, allowing us to represent clients in Maryland, including those in Anne Arundel County, Carroll County, Harford County, Howard County, Montgomery County, Prince George’s County, Queen Anne’s County, Maryland’s Western Counties, Southern Maryland and the Eastern Shore, as well as the communities of Catonsville, Essex, Halethorpe, Middle River, Rosedale, Gwynn Oak, Brooklandville, Dundalk, Pikesville, Parkville, Nottingham, Windsor Mill, Lutherville, Timonium, Sparrows Point, Ridgewood, and Elkridge.